Most quality anvils these days are either cast or drop forged and then hardened, drop forged anvils are only available up to 75kg. One recurring question from clients is about hardness and the answer to that question is quite complicated because hardness and quality do not always go hand in hand.
Although a relatively hard face is desired for longevity, an anvil with an overall hard face can be susceptible to broken/chipped edges. The quality and kind of the steel used in the anvil face has a lot to do with susceptibility to edge chipping.Some manufacturers like Refflinghaus rely on a very tough steel to resist edge chipping and others like Perun use a special steel alloy and temper the edges of their anvil faces so they are softer than the rest of the face to prevent the edges from crumbling. Unfortunately many modern anvil makers produce anvils with overall softer faces as it reduces edge chipping and makes them a lot cheaper to produce and many are made from cast iron (not steel) and are much too soft and break too easily for general blacksmith use.
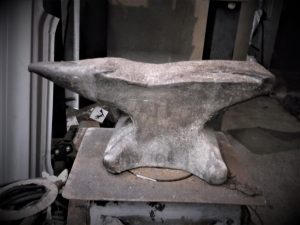
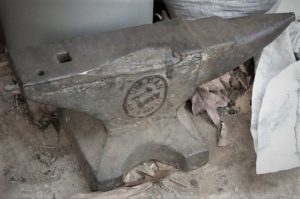
Hardening an anvil properly requires skill and expertise. Typical methods being used to harden anvils are flame hardening, induction hardening, heating the entire anvil in a forge, heating the top 1/3 of the anvil in a forge, etc. All these methods involve heating the anvil to critical temperature and then quenching in either water, oil or air. One of the biggest challenges to overcome, when heat treating an anvil is the tendency for the centre of the face to cool slower than the rest of the anvil during the quench, resulting in steel that is softer in the centre. The smaller the anvil, the faster it cools which is why some small anvils have very hard faces. By the same token, the bigger the anvil the greater the tendency for an overall softer anvil.
The best of the modern anvil manufactures have the steel composition and heat treating technology necessary to keep an even hardness over the face of the anvil no matter what the size. Some cheaper anvils have flame hardened faces which is a very shallow hardening process (typically less than 1/4"). The face might be relatively hard HRC54 to HRC56, but with use, the thin face will depress into the anvil body over time.So how do you determine if you are buying a quality product? I'm afraid there is only one way to find out and that is by destroying the anvil using a very hard file. The next best thing is to buy an anvil from a reputable manufacturer who has a long history producing high quality anvils.
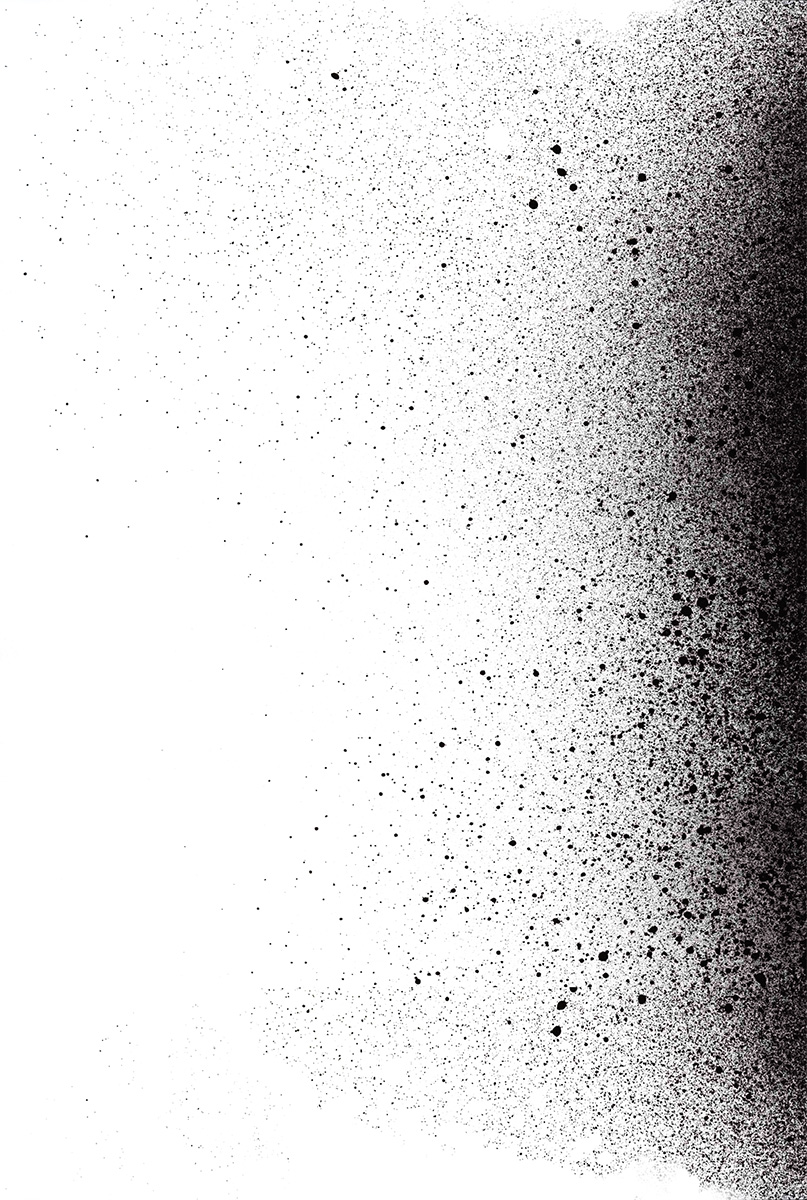